2008年08月01日
製造業における「トレーサビリティ」について(その2)
4.製造業における「トレーサビリティ」のポイント
工業製品の「トレーサビリティ」(製品トレーサビリティ)の歴史は古く、例えば戦前の日本で生まれた製番/号機管理などは「トレーサビリティ」の概念を持つものといえます。製造業では不良品・故障の原因追究などの品質管理、リコール対応などの安全管理といった目的で、製品や部品の個別管理への努力が行われてきました。近年ではさらにグリーン調達、リサイクル、環境規制による製品回収などに迅速に対応するため、製品に含まれる化学物質を考慮した「トレーサビリティ」の仕組みも要求されつつあります。そのため、従来のような製造工程だけではなく、材質・仕様等を含む設計情報の変更履歴などを確認できる、より詳細な製品構成の追跡管理を実現する「トレーサビリティ」の仕組みへの発展が必要となってきています。
ここでは、最近要求が強くなってきた製品構成の追跡管理に着目し、そのポイントについてご紹介します。
リコール対応や環境規制による製品回収等を行う場合、一般的に2つのステップで行います。まず初めに、「不具合理由の特定」を行います。これにより特定製品の不具合を生じさせている部品を特定します。次にその部品を使用している全製品洗い出し、対象製品を特定して行きます。これが、「影響範囲の特定」です。リコールを行うとすれば、この洗い出された製品が対象となります。それぞれのステップについて、これからご説明します。
4.1. |
不具合理由の特定 |
|
不具合理由の特定は次のような手順で行います。
(1) |
不具合製品を入手し、製品を特定する |
|
どのようにして製品を識別するかは、各社の事情・製品特個別品、量産品等)で異なりますが、一般的には、製品に記された型式・製造番号・ロット番号等識別番号が挙げられます。不具合製品の識別番号から製品の特定を行います。 |
(2) |
不具合の発生した製品の部品構成の入手 |
|
特に製品が組立品の場合は、部品構成の把握が重要になります。部品構成は、部品表の正展開から、求めます。その際部品は、部品番号で特定されることが一般的ですが、リビジョン・バージョンといった変更履歴レベルも含めた把握が必要となります。 |
(3) |
不具合部品の特定 |
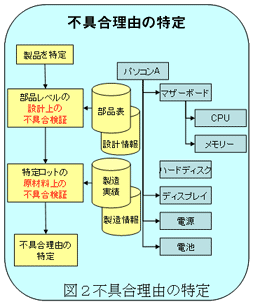 |
|
部品構成を元に、不具合状況から、不具合部品を特定します。上述のように部品番号・変更履歴レベルも含めた特定となります。 |
(4) |
不具合部品の設計情報の入手 |
|
特定された部品の設計変更履歴、図面、仕様等の設計情報を収集し、設計時点での仕様を明確にします。この際、迅速かつ精確に設計情報が検索できるように、PLM等の設計支援システムが準備されていることが求められます。 |
(5) |
設計面からの不具合理由の検討 |
|
不具合状況と設計仕様から設計面からの不具合理由を検討します。
設計面からの不具合理由がない場合もあります。 |
|
|
(6) |
不具合部品の製造情報の入手 |
|
いつどこから調達したどのような素材を使用して、いつどのように加工されて作られた部品かを示す製造情報を入手します。このときには、迅速かつ精確な製造実績や調達等の情報を含めた製造情報の参照が必須となります。これら情報が、ERP等の生産管理システムで収集管理されていることが必要となります。 |
(7) |
製造面からの不具合理由の検討 |
|
不具合状況と製造情報から製造面からの不具合理由を検討します。製造面からの不具合理由がない場合もあります。 |
(8) |
総合的に判断して、不具合部品と不具合理由を特定する |
|
不具合部品や不具合理由は複合していることもありますが、基本的には上記のプロセスで特定して行きます。
このプロセスを図示したのが、図2不具合理由の特定です。 |
|
4.2. |
影響範囲の特定 |
|
影響範囲の特定は次のような手順で行います。
(1) |
不具合部品と不具合理由を入手 |
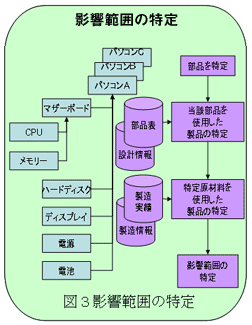 |
|
前項「不具合理由の特定」で特定された不具合部品と不具合理由を入手します。 |
(2) |
不具合部品を使用している全製品の洗い出し |
|
部品表の逆展開機能を用いて、不具合部品を使用している全製品の洗い出しを行います。設計面で不具合があった場合、ここで、洗い出されたすべての製品がリコール対象となります。原材料等の素材に理由がある場合は、さらにその素材を使用したかどうかの検討を行うことになります。 |
(3) |
特定原材料を使用した部品の特定 |
|
不具合部品の製造実績、製造情報を入手し、特定原材料を使用した部品の製造時期・ロット番号・製造番号等を調べます。これにより、該当部品を使用した製品の製造時期・ロット番号・製造番号等を特定します。製造面で不具合のあった場合、ここで特定した製品がリコール対象となります。 |
(4) |
影響範囲の特定 |
|
(2)、(3)のステップで特定された製品が、基本的には影響範囲となり、リコール対象となります。実際のリコールを行う際には、流通在庫も把握した上で、対応処置を行うこととなります。このプロセスを図示したのが、図3影響範囲の特定です。 |
|
|
|
「不具合理由の特定」や「影響範囲の特定」といった製品構成の追跡管理の仕組みを構築するポイントは、今までご説明してきたように、製品マスター管理であるPLMとトランザクション管理であるERPが連携し、情物一致を実現することにあります。図4でその概念を示します。
次回は、「トレーサビリティ」の仕組みを構築するメリットについて解説いたします。
|
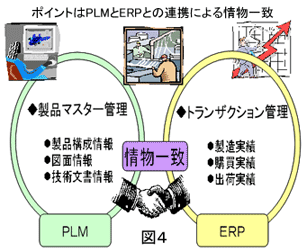 |
2008年8月